Manufacturers, fabricators and engineers of any size can use new affordable tools.
Manufacturers across the United States often outsource the fabrication of custom parts because they lack the equipment to make those parts themselves. Typically taking weeks to months to outsource custom parts or machining, many fabricators and engineers have had projects stalled and revenue impacted by long lead times. Add constant supply chain disruptions and difficulty predicting expenses to the outsourcing conundrum, and some are beginning to question the true cost-saving nature of outsourcing. Sidewall Conveyor Belt
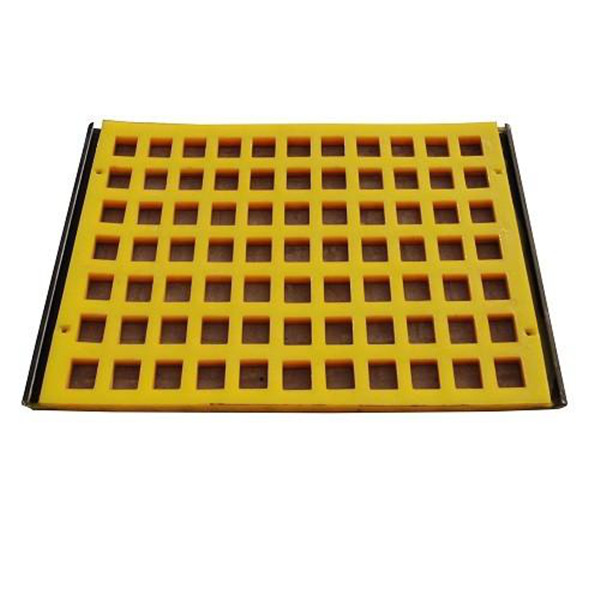
Many manufacturers expect the parts and processes that they outsource to be done on demand, yet many outsourcing suppliers have limited capacity and long wait times. This has led shops and labs to explore alternate options for outsourcing and achieving their timely production requirements. One solution to create and maintain such a workflow is to replace outsourcing by implementing in-house small-format digital manufacturing tools that are accessible and easy to use.
With the help of compact, affordable machines for subtractive and additive manufacturing, prototype iteration cycles are reduced, custom tooling is ready faster and low-volume manufacturing may be done in-house, reducing unnecessary downtime while slashing costs.
One such machine that is helping to reduce the reliance on outsourcing for many manufacturers is the waterjet cutter. Using high-pressure water mixed with abrasive particles, waterjets cut through sheet metal, plastic, composites, rubber and virtually any other material. Pairing these machines with additive tools like 3D printers, engineers and manufacturers have an incredibly versatile set of automated, modern technologies capable of keeping processes in-house.
Waterjets are not a new technology and have long been used in industrial settings. The issue is that waterjets tend to be large, expensive and hence out-of-reach for most people. But a new wave of affordable, desktop-sized machines is making waterjet cutting accessible and affordable to a much wider market than ever before, enabling work to be done in-house instead of being outsourced.
Reliance on outsourcing can prove costly for any engineer when prototyping. Prototyping requires flexibility and adaptability through every step by involving multiple iterations of a repetitive process that includes design, building, testing and evaluation. Outsourcing custom pieces will only negate an iteration cycle’s frequency and effectiveness as they must rely on external resources.
For example, a defense manufacturer needs short turnarounds for carbon fiber prototype parts. Their challenge is to produce small volumes of parts in a difficult-to-machine material like carbon fiber, when their lab may not have the technology or staff needed to work with these materials.
With desktop tools like waterjet cutters, engineers can create various carbon fiber parts in their shop without outsourcing any steps to vendors or suppliers. Supported by CNC waterjet machines, iteration cycles for carbon fiber parts are greatly accelerated while engineers maintain complete design control.
These prototypes are also typically more functionally useful, as engineers can produce them using the same material as the final part, enabling the prototypes to be tested for functionality. Typically, engineers using 3D printers and laser cutters have been limited by the materials these machines can work with. With waterjets, engineers can make functional prototypes using the desired material throughout iterations.
When appropriately maintained, industrial equipment can last decades. Of course, regular repairs will be necessary, which often require custom fabrication to replace old parts, or creating shims to ensure internal components fit together exactly as needed. Shops can either source the replacement parts and wait weeks or months, or have the capability to produce the replacement parts in-house needed to perform repairs.
If, for example, the bearings from a lathe needed to be shimmed to ensure proper preload, stocking every type of shim for every piece of equipment is unrealistic. Instead, manufacturers can use desktop machines like waterjet cutters to cut custom sheet metal and tool steel parts and shims. Having desktop subtractive manufacturing tools like a waterjet cutter that can cut shims or custom parts will inevitably save time and avoid the headaches of equipment downtime or outsourcing repairs.
No longer are the benefits of subtractive manufacturing restricted to only larger operations. Manufacturers, fabricators and engineers of any size can use new affordable tools like desktop waterjet cutters to overcome the burden of outsourcing. As the technology becomes more accessible, engineers and manufacturers can increase creative control on their projects while accelerating key processes.
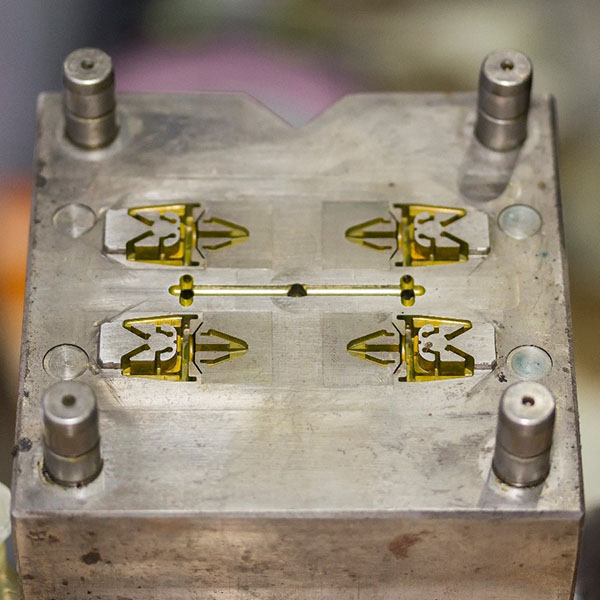
Slab Gate Valve Nisan Lerea is the Co-Founder and CEO of WAZER and an inventor of the world’s first desktop waterjet cutter. A consummate “maker,” Nisan spent many hours in the machine shop during his time at the University of Pennsylvania working on projects including a Formula 1-style race car. He needed to cut sheet metal but only had access to laser cutting, which could only cut soft materials. Nisan set out to solve the problem, inventing the first small-scale waterjet that would become WAZER. While working as a mechanical engineer, Nisan realized that other designers and engineers still faced barriers to waterjet cutting, so he teamed up with former colleague and fellow Penn Engineering student Matt Nowicki to launch WAZER in 2016.