There are gauges on fire pumps, internal fire protection systems, gauges for determining water flow, and meters used on electrical and certain hazardous atmosphere measuring equipment. There are also gauges designed to register hydraulic and air pressures. Perhaps it is not entirely realized to what extent gauges and meters enter into the decision-making process of a fire department’s operations.
Do You Understand Your Gauges? Fire Protection Jockey Pump
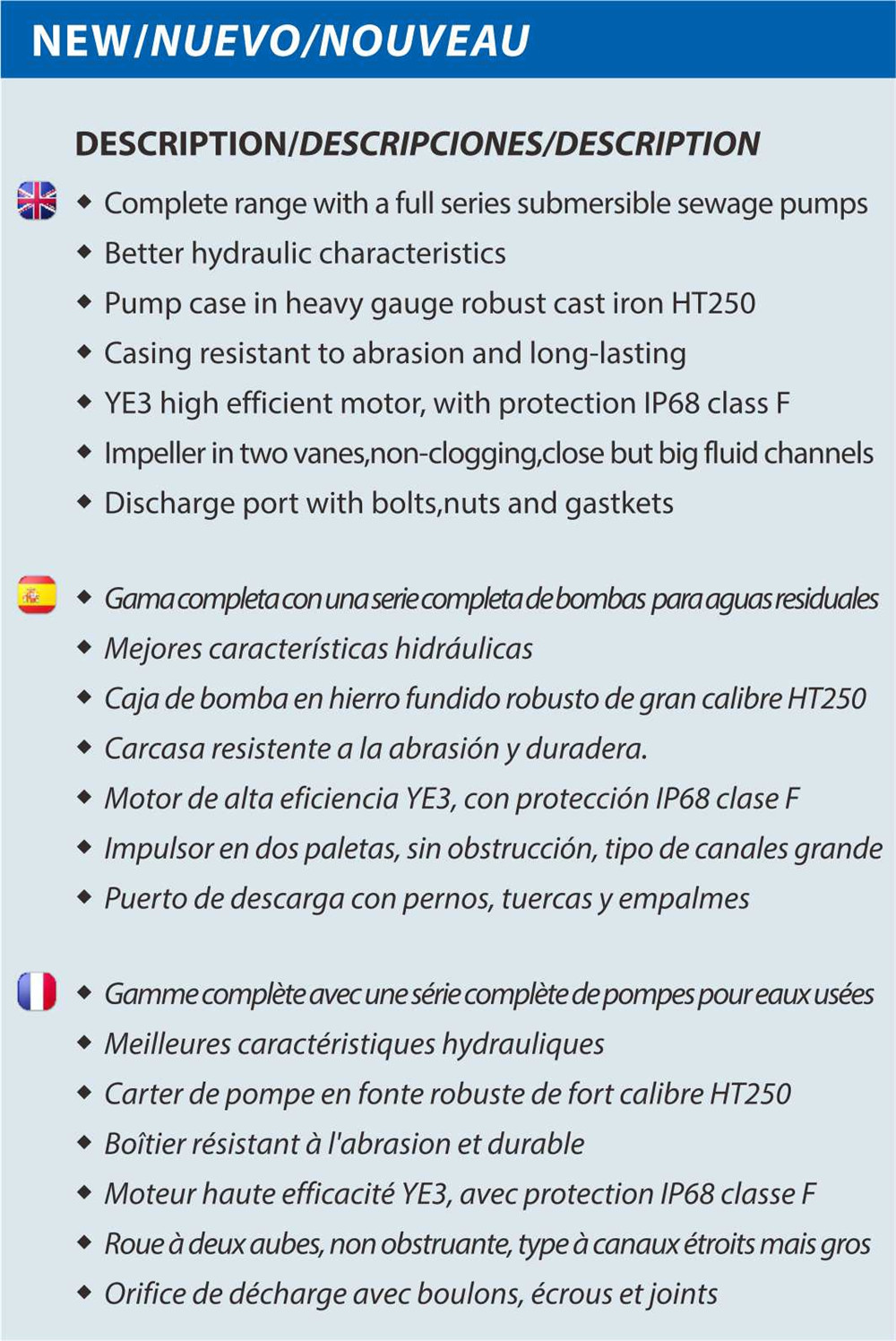
There are gauges on fire pumps, internal fire protection systems, gauges for determining water flow, and meters used on electrical and certain hazardous atmosphere measuring equipment. There are also gauges designed to register hydraulic and air pressures.
Perhaps it is not entirely realized to what extent gauges and meters enter into the decision-making process of a fire department’s operations. For the most part, readings or indications of these gauges and meters are accepted by field personnel as “unquestionable fact.” Based on the “gauge reading,” decisions are made that affect whether the quantity of water is sufficient at a certain hydrant, or whether a certain pumper is meeting its service test. Therefore, it is useful to review how to determine whether the gauge or meter being used for a measurement is appropriate for the task, and what the important considerations might be when reading a meter or gauge.
Certainly, it is understandable that if the pressure in a water system is in the vicinity of 200 pounds per square inch (psi), then a gauge with a full-scale indication of 150 psi is not appropriate. On the other hand, is it just as understandable that if critical measurements are to be made at 200 psi, then a gauge with a full-scale indication of 600 psi may be just as inappropriate?
A typical gauge consists of a closedin, curved tube (see figure 1). When pressure is imposed on the tube, the curved tube tends to straighten out, similar to the action occurring in a hose line when it’s charged. Through a series of mechanical connections, this tendency to straighten is translated into a rotary motion on a gear, which in turn is transmitted to a gauge pointer. Numbers printed in psi on the gauge face display the relative displacement of the curved tube. But the displacement, or straightening-out of the tube, for all pressures from zero to full scale, is not absolutely predictable from one tube to the next. So too, the mechanical reproducibility of the tubes is not exactly the same from one tube to the next. Actually, gauge faces are more reproducible than the tubes.
Bourdon tube pressure/vacuum gauge
A gauge is calibrated at full scale, or very close to full scale at the factory. This calibration involves placing a known, precise pressure on the gauge and adjusting a screw that controls the needle. This needle is then adjusted to read the known pressure. Therefore, it can now be understood that the full scale reading of the gauge can be meaningful and accurate.
Since the gauge will be used over a’ variety of temperatures under varying humidity and vibration conditions, the manufacturer is prepared to indicate to the purchaser that under most conditions, the accuracy of the gauge will be within plus or minus a certain percent. Generally, this is 2% or 3%, and is printed on the gauge or packing box. Now it becomes apparent that there is some amount of inaccuracy to be expected from any gauge.
But the heart of the matter is to determine what kind of inaccuracies are to be expected, how large they might be, and how these inaccuracies affect the usefulness of a gauge reading. Take a typical gauge that has as its fullscale reading 600 psi (see figure 2). If the accuracy published by the manufacturer is ±2% what does this mean about gauge readings? Two percent of 600 is equivalent to ±12 pounds (600 X 0.02 = 12). This implies that an indication of 600 psi on the gauge really means that the pressure is somewhere between 588 psi and 612 psi over a series of reading. It is noted that if this same gauge has an indication of 150 psi printed on the gauge face (see figure 2). How does the ±2% of full-scale factor for this gauge affect this reading? Unfortunately, one does not take 2% of 150 psi to find the possible range of readings. The 2% of 600 psi still applies. At the reading of 150 psi on the gauge, the actual pressure lies somewhere between 138 psi and 162 psi. Remember, the 12 psi, plus or minus, calculated applies at each and every indication throughout the scale. It is obvious that the difference between 138 and 162 psi can create a significant difference in fire streams, or can yield a significant difference in apparent pump performance. On the other hand, if the gauge on the pumper had a full-scale reading of 300 psi, then the 2% error would be reduced to only ±6 psi, or 144 psi to 156 psi.
If one continues to consider fire pumper gauges for a bit longer, it may be noted that there is an increasing tendency for the discharge gauge and the compound (inlet) gauge to be identical in type and range upon purchase of apparatus (see figure 2). A compound gauge is one that can indicate both positive and negative pressures relative to atmospheric pressure. While there is no doubt that a logistic and dollar reason exists to keep all the gauges the same, it must be obvious by now that the readings on the compound gauge will be less meaningful than those on a similar discharge gauge. This is because of the general lower pressure range of operation of a typical inlet gauge. Much of the compound gauge operation is in the 20 psi to 50 psi region. Again assuming that the gauge is a ±2% of full-scale design, the error at 20 psi on the gauges in figure 2 can be ±12 psi. The experienced pump operator, now that this fact is understood, does not dispair. In the real world, the critical operational pressure indications, for the most part, are found on the discharge gauge.
Why is a particular full-scale reading selected?
National Fire Protection Association Standard 1901, Automotive Fire Apparatus, states that the recommended full-scale indication for the major pump gauges should not read less than 300 psi full-scale, and not more than 600 psi full-scale. All too often, purchasers select the 600 psi indication because of a lack of understanding of the actual expected operating pressures for the pumper being purchased. Except for special apparatus, operation of pumpers above 250 psi discharge is not common.
When testing pumpers, it is important to understand the limitations of the discharge gauges. All too often, pumpers are service tested from draft with 150 psi indicated on the discharge gauge. This is almost always an incorrect gauge reading by any reasoning. Most often, the actual desired pressure is 140 to 146 psi. A gauge error of 12 psi in the positive direction will insufficiently load the pumper; an error of 12 psi in the negative direction can cause a pumper to appear inadequate. For this reason, fire departments wishing to make serious evaluations of their pumpers use specially calibrated, carefully maintained gauges as the measuring instruments. The measurement of the inlet pressure (compound pressure) during a service test is oftentimes measured with an open-tube manometer. There are connections provided on pumpers for making this measurement. These connections are above the two main gauges. This is where open-tube manometers and specially calibrated gauges are attached to the pump.
While on the subject of service testing pumpers, it is important to point out that the full-scale reading of the pitot gauge is also critical. The pitot gauge (impact tube) is used to measure the total pressure of flowing fluids (such as nozzle discharge) by converting the velocity energy to pressure energy. Similar errors in measurement can creep into the volume discharge of the nozzle measurement if the full-scale reading of the pitot gauge is too high compared to the expected pressure. For example, if the full-scale reading of the pitot gauge is 120 psi with ±2% of fullscale accuracy, then the error would be ±2.4 psi. Now, 50 psi across a 1 ½-inch straight tip yields 465 gpm. However, considering error, the indicated gauge flow could be a real flow of anywhere from 455 gpm to 480 gpm. But this possible error could be significantly reduced if a gauge with a full-scale reading of 60 psi, same accuracy, were used. 1’wo percent of 60 psi is ± 1.2 psi. Going through the same calculations, the spread of possible flows would be reduced to between 462 psi and 474 psi.
The foregoing discussion should demonstrate the value of properly selecting the full-scale reading of a gauge. As a rule of thumb, try to select a test gauge so that the expected or needed test reading in psi falls in the top third or quarter of the gauge or meter. Particular care should be taken in the selection of gauges for use in testing water systems and hydrant flows. The pressures encountered in these instances are generally relatively low. Remember in the field that if the needle is indicating anywhere in the lower third or quarter of the gauge, the inaccuracies will begin to increase notably, yielding data of questionable value.
In summary, testing procedures yield data that is used to draw some conclusion. The quality of the conclusion is only as good as the accuracy of the data and the care taken in obtaining the data. Testing of fire pumpers, water systems, and fire flows, and acceptance of internal fire protection systems all require an understanding of measurement techniques and good judgment on the part of the data taker. When working with the private sector, i.e., engineers and technicians, it is common for these individuals to be very sensitive to proper testing procedures. Don’t embarrass yourself or your profession by not being knowledgeable of the care to be exercised in taking measurements.
Stay in the know with the latest content, features, and training from the largest online firefighting community.
Please check your spam folder and any email filters, in the event that the email gets blocked.
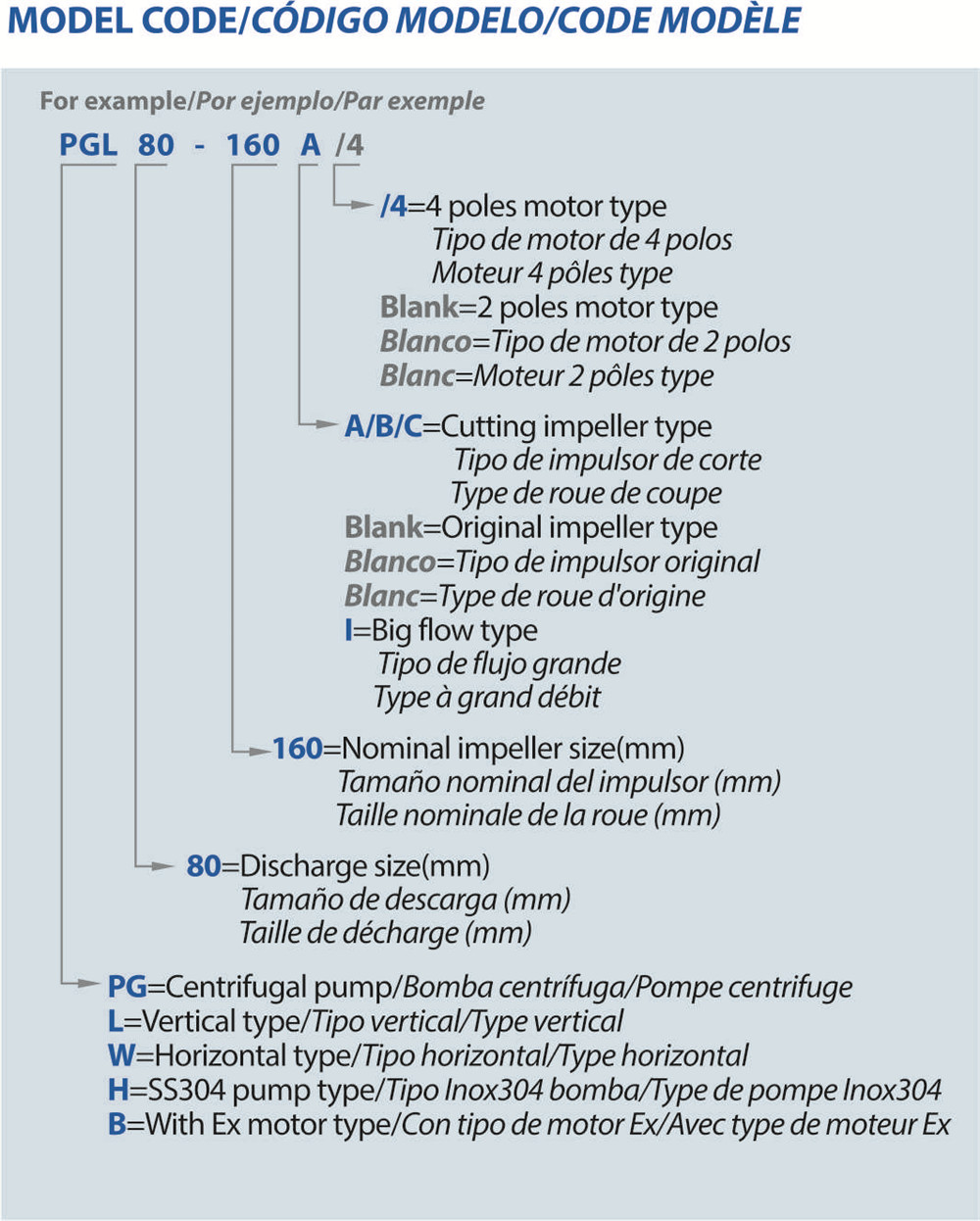
Non-Negative Pressure Water Pressure Booster System Stay informed about daily FireEngineering news, podcasts, training videos, webcasts, commentary, and exclusive articles about FireEngineering by signing up.