This article was updated May 25, 2023. It was originally published Nov. 17, 2009.
To put hard, durable threaded holes in plastics, engineers often specify threaded metal inserts that will securely hold fasteners and reinforce joints. Though stainless-steel inserts may work well, using them is often overkill and unnecessary. Brass inserts, on the other hand, meet most performance requirements and offer significant cost benefits compared to steel. Stainless Steel Nut
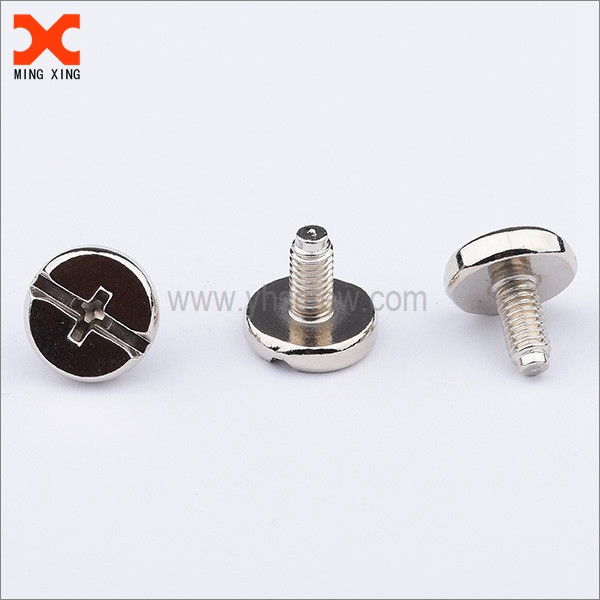
Raw material costs for brass and stainless steel are typically similar but it costs much more to machine stainless steel. Free-machining stainless steel may only be 40 to 50% as efficient to machine as brass. And other austenitic stainless steels may be less than 40% as efficient to machine. One aspect of stainless steel’s lower machinability is that it is a poor conductor of heat compared to brass. This raises temperatures during machining and reduces the life of cutting tools.
Brass scrap created during machining can be sold with a minimal loss in value. In contrast, stainless-steel scrap retains little of its initial value, which is another reduction in overall efficiency.
Machined inserts can be installed using several different methods, though post-mold heat installation is the most common. Inserts can be heated several ways: charged directly using heated tips or chimneys, or indirectly with ultrasonic energy. In both methods, the insert must be heated to at least the plastic’s melting point.
A mentioned earlier brass is much better conductor of heat than stainless steel or carbon steel. In fact, it’s twice as conductive as carbon steel and 15 times more conductive than austenitic stainless steel. This allows more rapid heating and cooling when installing them in thermoplastics using heat, and this improves cycle time.
More rapid dissipation of heat also improves the insert’s positional accuracy. Rapid cooling prevents a condition commonly referred to as “float.” It arises when inserts remain hot after the tips or ultrasonic horn have been removed and the inserts move slightly. With fast cooling, the plastic sets quickly and fixes the insert accurately in position and depth.
Brass offers significant advantages over stainless steel, so it is preferred for most industrial and agricultural applications. But there are applications which require stainless steel. For example, brass and stainless steel both resist corrosion, but they react differently to various corrosive agents, so steel may get the nod in some instances.
Here’s a closer look at some of brass’ advantages:
300 Series and austenitic stainless steels are the most commonly used steel alloys for inserts, though many of the could also be used.
Among stainless steel’s advantages:
Putting Inserts in Plastic Parts: Ultrasonic or Heat?
The Fredsert: a Threaded Insert Tough Enough for the Marines

Thread Cutting Screw Michael Pasko was an application engineer at Spirol when this article was originally published.